Snowflake Ice: A Cool Business with Hot Competition
The vending machine business is evolving fast, and snowflake ice vending machines are right at the center of it. Whether placed near convenience stores, train stations, or coastal markets, they offer quick access to finely shaved ice for drinks, seafood preservation, or desserts like kakigori.
But as more operators enter the space, one thing becomes clear: not all machines are created equal.
Many vending machine owners—especially those running older or generic models—start facing problems within just a few months: clogged nozzles, broken payment systems, inconsistent ice production, and worse. And these aren’t just technical issues. Every jammed nozzle or failed transaction is a lost sale—and a frustrated customer who might not come back.
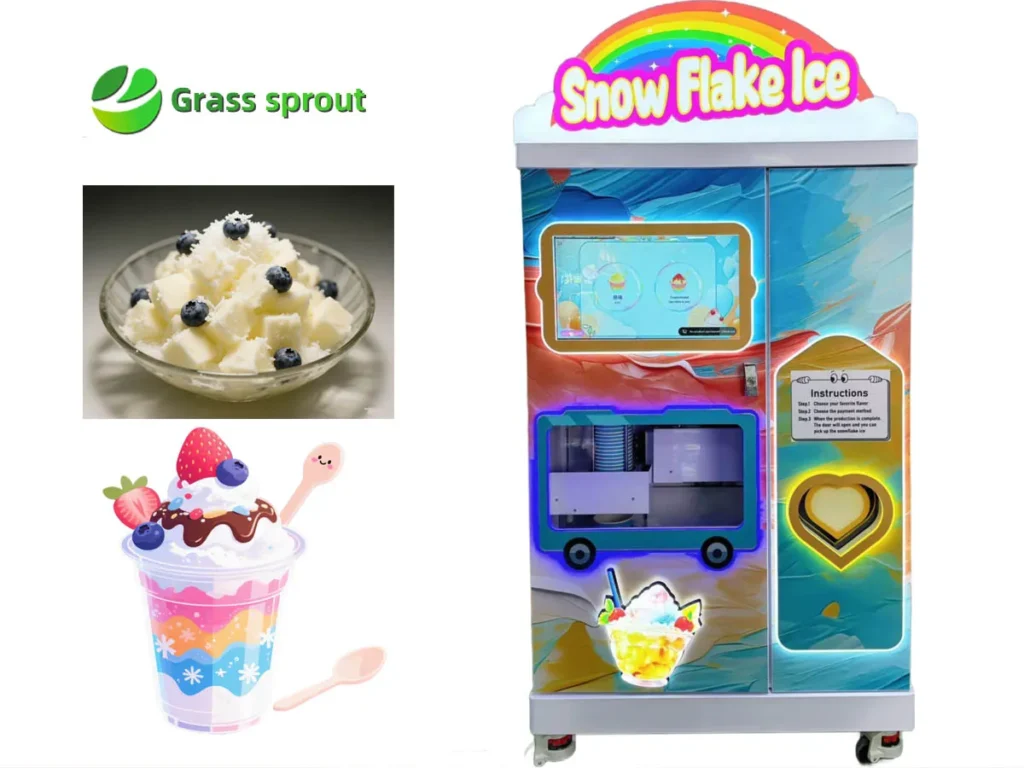
What Typically Goes Wrong
One of the most common issues is with the ice nozzle. Over time, mineral deposits from hard water and leftover ice particles can clog the dispensing system. Customers hit the button expecting clean, fast ice—but instead get nothing, or worse, a slow trickle followed by a loud mechanical grind.
Another common frustration? Payment failures. If the machine doesn’t accept a card, or if the QR code doesn’t scan, the customer walks away. This is especially problematic in countries like Japan, where mobile payments like PayPay or LINE Pay dominate.
Then there’s temperature control—a crucial but often overlooked issue. Ice that isn’t kept consistently frozen starts to melt and clump together, creating both a mechanical and hygiene nightmare. On the hottest summer days, some machines simply can’t keep up.
Add in touchscreen malfunctions, unstable internet connections, or full-blown system crashes, and suddenly your “passive income” machine is anything but passive.
So… We Built Something Better
When we designed our snowflake ice vending machine, we started by asking a simple question: What actually causes machine failure—and how can we design around it from day one?
Our engineering team interviewed field technicians, operators, and end users. We didn’t want to just solve these problems—we wanted to prevent them altogether.
Self-Cleaning, Anti-Clog Nozzles
Instead of waiting for ice to jam the system, our machine performs automatic nozzle cleaning cycles throughout the day. After every set number of uses, the machine flushes the internal tubing using food-safe water pressure. Combined with an anti-stick interior coating, this virtually eliminates mineral buildup and blockage.
The result? Smooth ice delivery every time—without a technician visit.
Payment That Always Works
We’ve seen too many operators lose revenue over something as simple as a dropped Wi-Fi connection. That’s why we built dual-network redundancy into every unit—our machines switch seamlessly between Wi-Fi and 4G LTE based on signal strength. They also support major local and global payment providers: from IC cards to WeChat Pay to Visa.
On the backend, we offer remote diagnostics, so any hiccup in the payment flow can be fixed without physically touching the machine.
Smart Cooling that Adjusts in Real Time
Temperature control is non-negotiable in the ice business. That’s why our system features a dual-compressor setup and an AI-powered thermostat that adjusts based on ambient weather. If the outside temperature spikes, the machine increases cooling efficiency automatically. It even tracks usage trends to boost ice output during rush hours and dial it back at night.
This not only keeps your ice in top condition—it also saves energy.
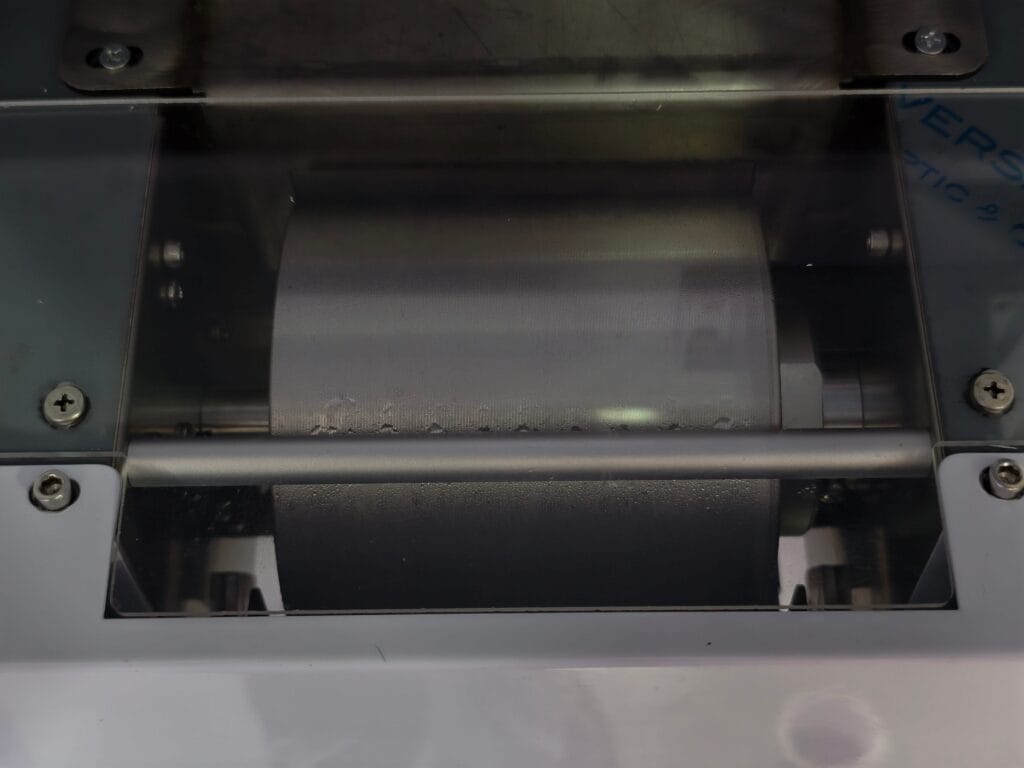
Touchscreens That Don’t Quit
We know what happens when a touchscreen goes down—your sales stop. That’s why we use industrial-grade, waterproof panels with anti-fog glass and humidity sensors. And in case something does go wrong, our machines can operate in fallback mode, letting users complete a transaction with minimal UI interaction.
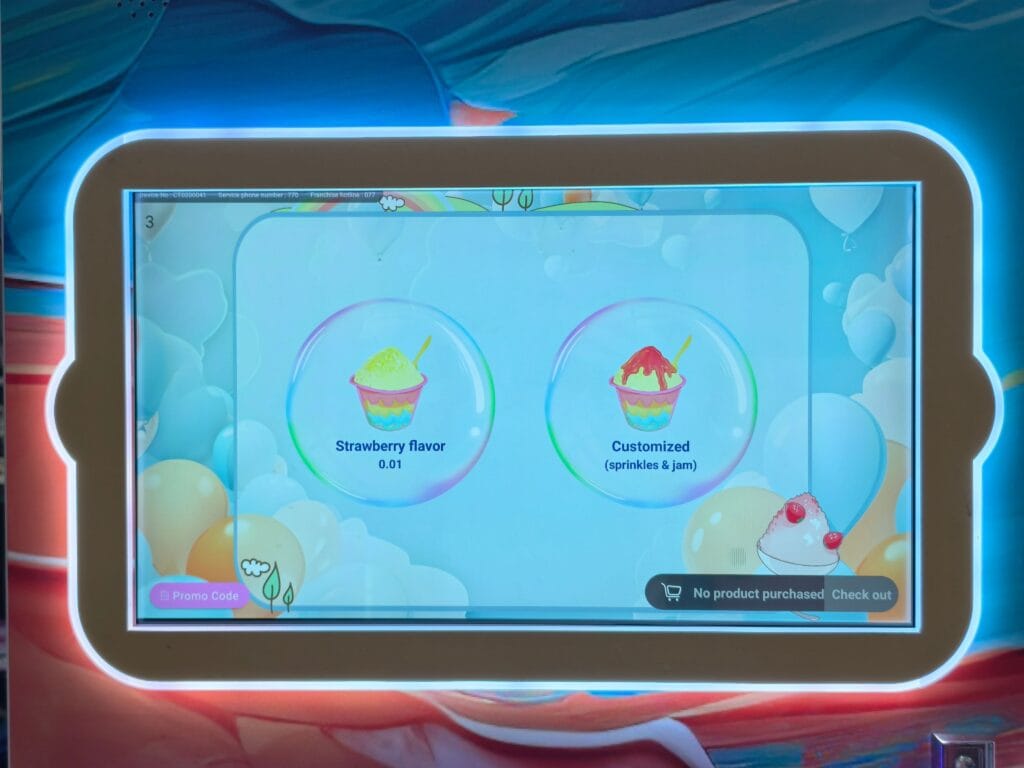
Less Ice Build-Up, More Performance
Frost inside the chamber can wreak havoc on internal parts. Our fix? A combination of scheduled defrosting, sloped drainage design, and ambient humidity sensors. These systems work together to keep moisture low, prevent internal build-up, and avoid damage to internal motors and gears.
All Managed Remotely
Perhaps our biggest leap forward is in our cloud-based control panel. From your phone or desktop, you can:
- Check sales performance
- View real-time ice levels
- Monitor internal temperatures
- Remotely reboot or update the system
You get full visibility without ever visiting the machine.
Looking Ahead: Designed for the Long Haul
Too many vending machines are built for short-term profit. Ours is designed for longevity and scalability.
We’ve minimized the number of moving parts. Chosen components rated for long-term outdoor use. Built in the logic to anticipate failure, not just respond to it. And because our machines are modular, replacing or upgrading parts takes hours, not days.
Looking for a Snowflake Ice Vending Machine that won’t let you down?
Our smart, self-cleaning system is built to handle high demand, harsh weather, and the tiniest maintenance schedule.
👉 Contact us today to learn how you can install a next-generation machine at your location.
Related Posts
- 🎡 How Long Does It Take for a Cotton Candy Vending Machine to Start Making Cotton Candy?
- Mobile Phone Case Printer vending Machine: A Smart Investment for Creative Entrepreneurs?
- Is an Ice Vending Machine Profitable? A Deep Dive with Snowflake Ice Vending Machines
- Where Can You Make Your Own Phone Case? Try a Phone Case Printing Vending Machine
- What Machine Do You Need to Print Phone Cases? The Answer Lies in Self-Service Innovation
- Are Cotton Candy Machines Messy? Not Anymore – Here’s Why Modern Vending Machines Are a Game-Changer
- Can You Put Regular Sugar in a Cotton Candy Machine?
- Is a 3D Printed Phone Case Safe? Absolutely – Especially with UV Printing Technology